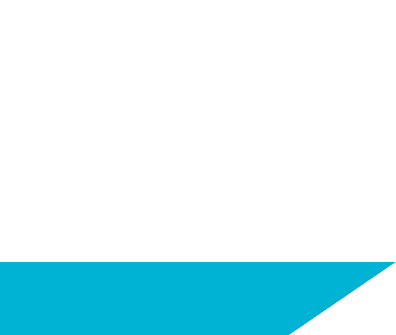

Consistency
Product quality maintained from start to finish at all times
On Site
Experienced on shore QCs teams guarantee quality before shipment

QC From Start To Finish
From materials to transport we have you covered
Quality Control You Can Count on,
from Prototype Through Production
Quality Control
Custom fixture manufacturing, no matter the size of the project, has many inputs that can affect the final product. Variables like the quality of the raw materials, labor disruptions or port congestion can at any point have a detrimental impact on your custom fixture project. That is why S-CUBE Fixtures has a Shanghai based quality control office staffed with local project managers and full-time certified QC engineers to make sure your projects run smoothly without any surprises. With in-place monitoring and reporting processes that adhere to stringent guidelines & control processes you can be assured that we guarantee consistency of product from prototype through production.

Looking Out For You, The S-CUBE Way
Quality Control involves all parts of manufacturing process. We begin with testing raw materials, pull samples from the manufacturing line, and ensure the finished product is everything like the approved prototype and drawings.
-
Our manufacturing partners train employees in latest international QC standards
-
Perform random equipment use tests to ensure production consistency and quality standards
-
Our QC teams use technology such as videos and remote monitoring to enhance and monitor Quality Control
-
Our QC team has rapid response plans documented and can quickly execute them once a defect is discovered to address the issue.
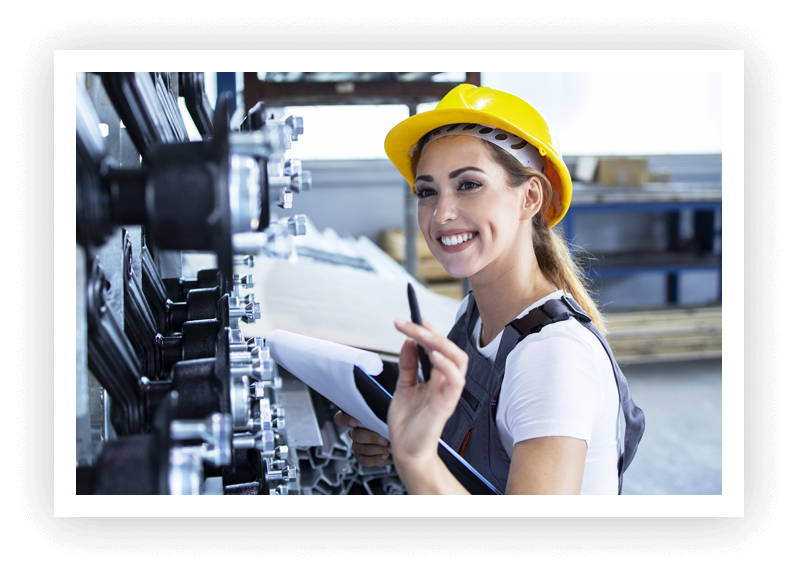
See Our Work. Here are a Few Examples to Help Inspire Your Next Project.
Fixtures were redesigned & value-engineered to speed manufacture, simplify assembly & reduce set time.
Domestically manufactured to meet first store dead-lines and then transitioned to overseas production to reduce costs.
Resources for Creating a Successful Retail Environment
Chat with Jeff or Kevin
Tell us about your project to get started.
Our team of industry veterans can share strategic insights, explore options and challenge costs to deliver exceptional client solutions.
Frequently Asked Questions
What is complete quality control in manufacturing?
Complete quality control in manufacturing refers to a comprehensive system that ensures every product meets specified standards before reaching the customer. It covers the entire production process—from raw materials and assembly to final inspection and packaging. This approach prevents defects, reduces waste, and maintains consistency in product quality. By using standardized protocols and inspections at every stage, companies can deliver reliable products, minimize returns, and meet customer expectations for durability and performance.
Why is quality control important in store fixture production?
Quality control is vital in store fixture production because fixtures must be both visually appealing and structurally sound. A poor-quality fixture can damage a brand’s image or pose safety risks. Consistent quality ensures that fixtures meet design specifications, function as intended, and align with brand aesthetics across locations. Rigorous inspection processes help identify issues early, reduce rework or replacements, and ensure fixtures are installation-ready, enhancing the overall retail experience and efficiency.
What processes are included in complete quality control?
Complete quality control typically includes incoming materials inspection, in-process checks, dimensional verification, visual inspections, functional testing, and final product audits. It may also involve documentation review, compliance checks, and packaging assessments. These steps ensure that products meet technical specifications, industry standards, and client expectations. Advanced quality control programs may also use statistical process control, ISO standards, and digital tracking systems for transparency and continuous improvement across the supply chain.
How does quality control reduce production costs?
Quality control reduces production costs by identifying issues early in the process, which minimizes rework, scrap, and customer returns. Catching defects before full production or shipment saves on materials, labor, and logistics. It also improves workflow efficiency and product consistency. In the long term, strong quality control systems lower warranty claims, protect brand reputation, and enhance customer satisfaction—resulting in fewer costly disruptions and better operational performance.
What tools are used in quality control for fixtures?
Quality control for fixtures often uses tools like calipers, gauges, measuring tapes, load testers, and visual inspection templates. Digital tools like barcode scanners, quality tracking software, and 3D measurement systems may also be employed. These tools verify dimensions, finishes, structural integrity, and material quality. Additionally, inspection checklists and photographic documentation help ensure that every fixture meets design and safety requirements before approval for shipping or installation.
How do you ensure consistency across large fixture orders?
To ensure consistency, quality control teams use standardized procedures, inspection protocols, and reference samples throughout the production run. Fixtures are reviewed at multiple stages to confirm adherence to approved designs and materials. Training programs for staff, routine audits, and documented quality benchmarks maintain uniformity. For large-scale orders, batch sampling and digital inspection reports ensure that even high-volume production meets brand specifications and passes all required quality standards.
Can quality control services be customized to my brand requirements?
Yes, quality control services can be fully customized to meet your brand’s specific needs. This includes tailoring inspection checklists, tolerance levels, visual standards, and packaging protocols to align with your fixture designs and retail environment. Custom QC programs may also include client-specific reporting formats, branded labeling requirements, and performance testing criteria. By aligning quality control with your branding and operational goals, you ensure your store fixtures consistently represent your brand vision.
How does your team handle defective or non-compliant fixtures?
If a fixture fails quality checks, it is flagged and removed from the production or packing line. The issue is then analyzed to determine the root cause—whether it's a material defect, design deviation, or production error. Depending on the findings, the fixture may be reworked, repaired, or scrapped. The quality control team communicates with production staff to correct the issue and prevent recurrence, ensuring only compliant, installation-ready fixtures are shipped to clients.